Molten Metal Filtration
Reasons for Molten Metal Filtration:
Solid impurities often found in molten aluminum can damage the final cast metal product.
These entrained solid impurities usually come from three aspects:
*The floating oxide layer on the surface of the molten aluminum draws aluminum oxide particles into the flow.
*The flowing aluminum stream erodes and entrains debris from furnace linings, troughs, and other aluminum handling equipment components.
*Some are precipitates of insoluble impurities, such as intermetallic compounds, borides, carbides, or other aluminum compounds, such as chlorides.
When these inclusions appear in the final cast product after the aluminum molten solidifies, they can cause the final product to have reduced ductility or poor finished product properties. Therefore, before the molten aluminum stream is cast into a solid body, it is best to remove the entrained solids in it for direct use or for forming operations such as rolling, forging, extrusion, etc.
The filtration process to remove entrained solids in a liquid is to pass the liquid containing solids through a porous filter medium, while the solids cannot pass. Generally speaking, filtering molten metal, especially molten aluminum, creates special problems because the liquid is very corrosive, and it is difficult to find filter media that can withstand it.
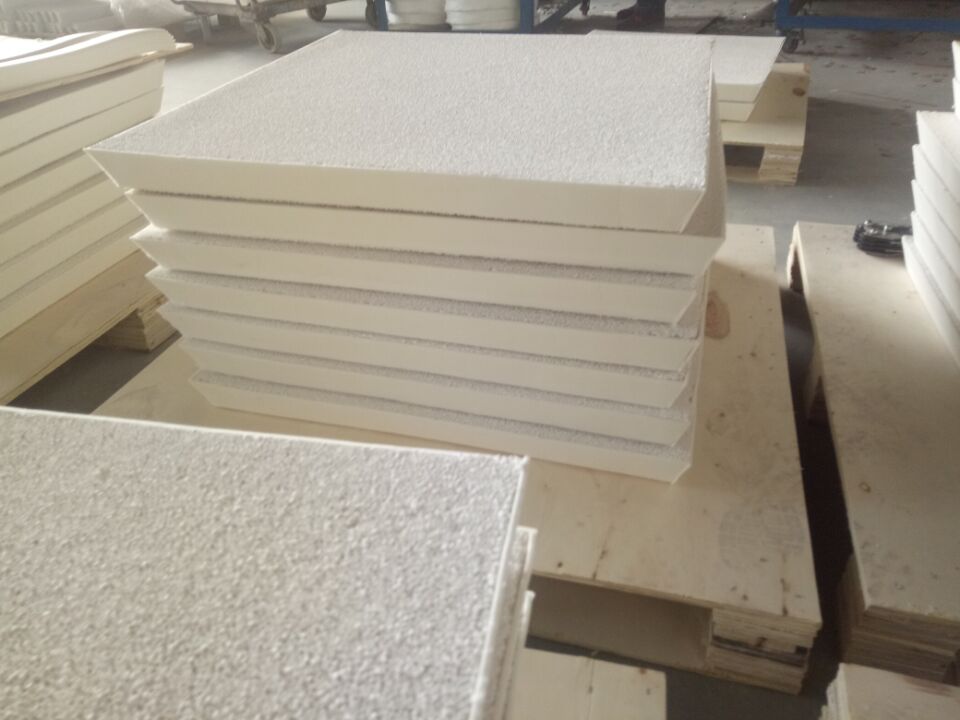
Molten Metal Filtration
Adtech ceramic foam filter is a high-purity alumina-based product.
Molten aluminum has high strength at high temperatures, long service life, and is heat-resistant and corrosion-resistant.
Ceramic foam filter is suitable for aluminum die casting, aluminum extrusion casting, etc., for filtering and adsorbing aluminum molten inclusions.
Adtech ceramic foam filter‘s advantages:
1 Multiple sizes and grades are available
2 High thermal shock resistance
3 Heat and corrosion resistance
4 Reduce waste pollution
5 Long service life
6 High impurity removal efficiency and good effect, improve the purity of molten metal, and thus improve the quality of castings